We may earn revenue from the products available on this page and participate in affiliate programs. Learn more >
When it comes to choosing materials, the decision to use steel can greatly impact the durability, functionality, and cost-effectiveness of various applications. Among the many options available, high carbon steel is known for its reliability, providing a solution for achieving top performance. If you’re struggling with selecting the right steel for your project, you’ve come to the right place.
Table of Contents
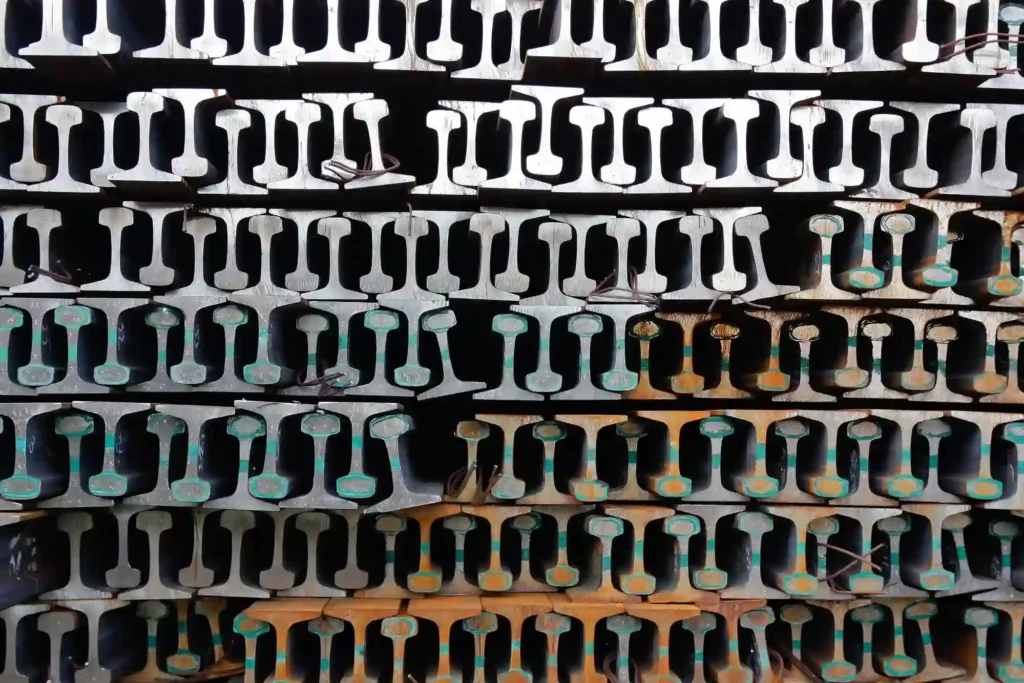
High carbon steel stands out from other steel varieties because of its increased carbon levels, resulting in greater hardness and strength.
This resilience has made high carbon steel blades highly desirable for their reliability in both combat situations and daily tasks.
This specific trait contributes to the exceptional durability of high carbon steel blades, allowing them to withstand tough conditions without sacrificing longevity.
Edge Retention and Sharpness
One of the standout features of high carbon steel is its impressive capability to maintain a keen edge. Blades crafted from this material are known for their long-lasting sharpness, facilitating accurate and efficient slicing and stabbing.
This sharp edge plays a crucial role in bladed weapons, significantly influencing the result of a conflict through enabling quick and impactful attacks. The durability and sharpness of high carbon steel make it a favored choice for weapons used in combat situations.
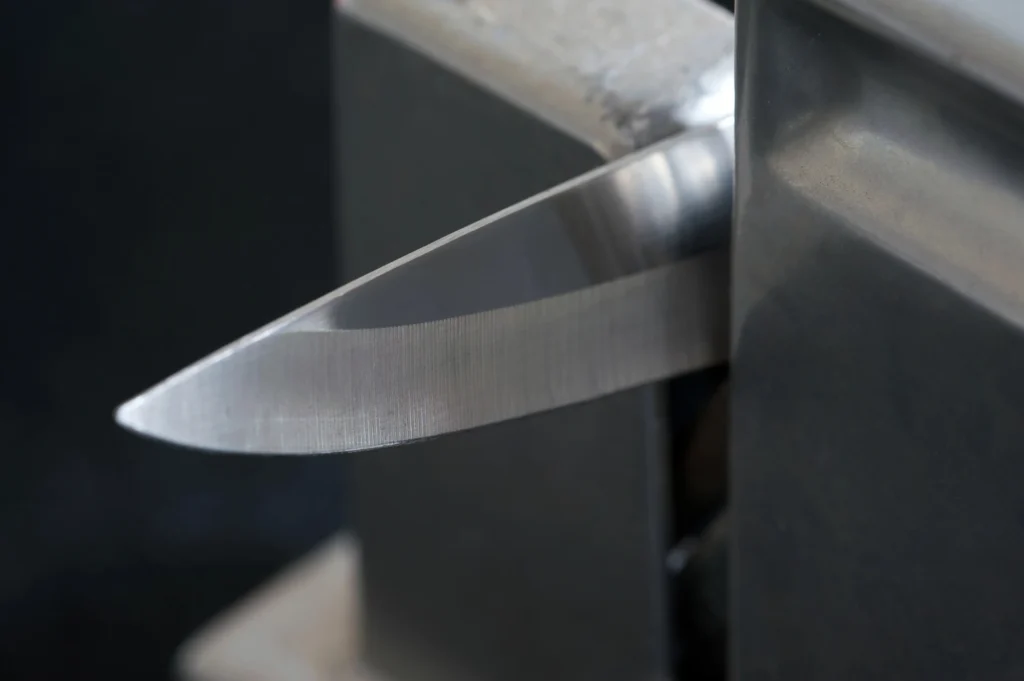
Flexibility and Resilience
Although high carbon steel is known for being incredibly hard, it also possesses a notable amount of flexibility. This flexibility is beneficial because it helps blades endure impacts and stress without breaking or becoming misshapen.
The durability of high carbon steel guarantees that bladed weapons will continue to perform effectively and consistently, even when facing intense use during combat scenarios.
Forgeability and Workability
The forgeability and workability of high carbon steel are highly impressive. Experienced craftsmen can skillfully shape this material into detailed blade designs, taking advantage of its flexibility to produce weapons that are both practical and visually appealing.
The precision and finesse required to manipulate high carbon steel has been a defining characteristic of blade making for generations.
Advantages | Disadvantages |
---|---|
High hardness for lasting durability. | Vulnerable to rust if not properly maintained. |
Maintains sharp edges for longer periods. | Difficult to shape due to its hardness. |
Strong and resilient for various applications. | Higher cost compared to other materials. |
Versatile use across different industries. | Prone to brittleness if improperly treated. |
Customizable properties through heat treatment. | Less flexible compared to some other metals. |
Resists impacts and shocks, increasing lifespan. | Requires careful handling to prevent breakage. |
Blade Making and Craftsmanship
The art of making blades from high carbon steel follows a long-standing tradition that demands expertise, accuracy, and a thorough knowledge of metallurgy. Each stage in the blade production process plays a crucial role in determining the overall quality and functionality of the end result, from choosing the raw materials to the final refinement of the blade’s surface.
Material Selection
Blade manufacturers start by meticulously choosing top-notch high carbon steel for their work. The carbon level in the steel, combined with various other alloying elements, impacts the blade’s toughness, flexibility, and other physical properties.
Bladesmiths typically opt for particular high carbon steel grades depending on the planned purpose and preferred attributes of the final blade.
Forging
The forging process is essential in the production of blades, as it involves heating raw steel to high temperatures and shaping it using traditional methods. High carbon steel is preferred for its ability to be forged and molded easily by bladesmiths.
Throughout the forging process, the heated steel is carefully manipulated with hammers and anvils to achieve the desired blade shape and profile. Controlled heating and cooling cycles are employed to enhance the steel’s metallurgical structure and improve its mechanical properties.
This process, known as heat treatment, is vital in achieving the right balance of hardness, toughness, and edge retention in the final blade product.
Shaping and Grinding
After the blade is formed, careful shaping and grinding are done to perfect its overall shape and cutting edge. Bladesmiths use a mix of hand tools and grinding machines to eliminate extra material and reach the desired thickness and curve of the blade.
This step demands accuracy and focus to guarantee consistency and balance in the final blade.
Heat Treatment
After carefully molding and refining the blade, it must go through one last crucial step: a final heat treatment process that enhances its strength and durability.
This vital stage includes heating the blade to specific temperatures before rapidly cooling it in either oil or water to create a hardened structure. Following this, tempering processes are employed to reduce internal stresses and enhance the blade’s ability to withstand impacts and bending.
Finishing Touches
The last steps in the process of creating a blade focus on perfecting its appearance and functionality. This includes tasks like polishing, sharpening, and adding protective coatings or decorative elements.
Bladesmiths pay close attention to improving the finish of the blade and ensuring its edge is sharp to not only make it visually appealing but also enhance its overall performance.
Types and Grades of High Carbon Steel
High carbon steel consists of a variety of alloys, each with their own distinct composition and characteristics. It is important to be familiar with the various types and grades of high carbon steel in order to choose the appropriate material for certain blade-making tasks and uses. Now, let’s delve into some of the popular types and grades of high carbon steel.
1095 High Carbon Steel
The 1095 steel stands out as a commonly utilized high carbon steel in the production of blades. With a carbon content of around 0.95%, this steel is recognized for its high hardness and ability to maintain sharpness.
Bladesmiths often prefer 1095 steel due to its uncomplicated heat treatment process and its capacity to achieve and sustain a keen edge.
Knives made from 1095 steel are highly regarded for their strength and lastingness, which explains why they are frequently chosen for tanto blades, survival knives, and hunting knives.
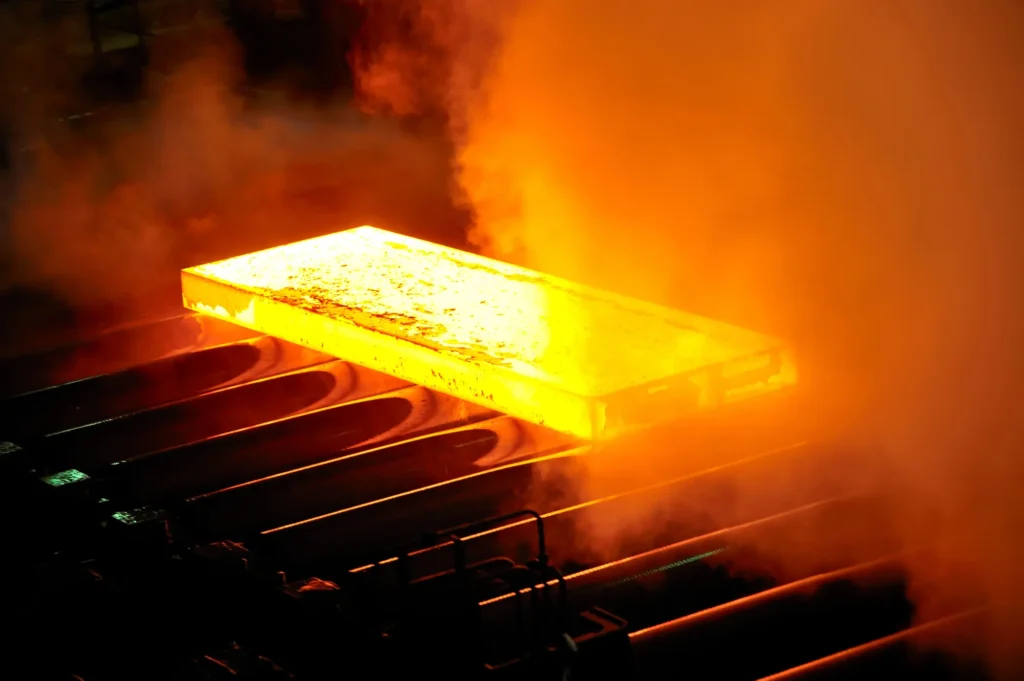
5160 Steel
5160 steel is an incredibly popular high carbon alloy celebrated for its outstanding toughness and resilience.
With a carbon content ranging from approximately 0.60% to 0.70%, as well as trace amounts of chromium and manganese, this alloy is renowned for its exceptional durability and shock resistance.
It is a top choice for crafting swords, machetes, and large chopping knives that require unrivaled toughness and impact resistance.
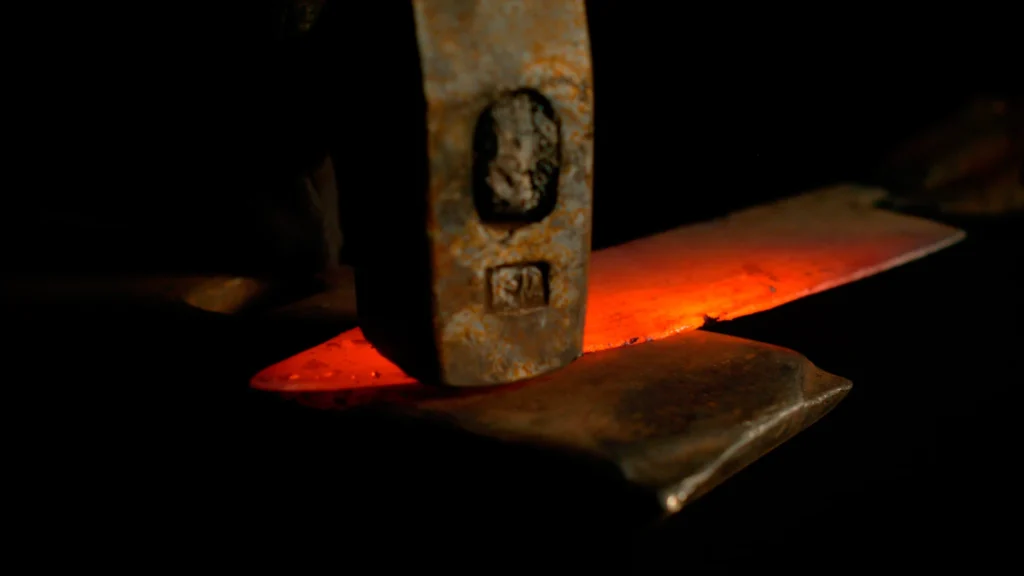
1084/1085 Steel
1084 and 1085 steels are exceptional high carbon alloys, boasting a carbon content between 0.80% and 0.90%. Bladesmiths highly prefer these steels due to their effortless forging and heat treating, along with their exceptional capability to maintain a razor-sharp edge.
Renowned for their versatility, 1084/1085 steel is frequently utilized in the creation of a wide array of blades, encompassing hunting knives, kitchen knives, and bushcraft tools.
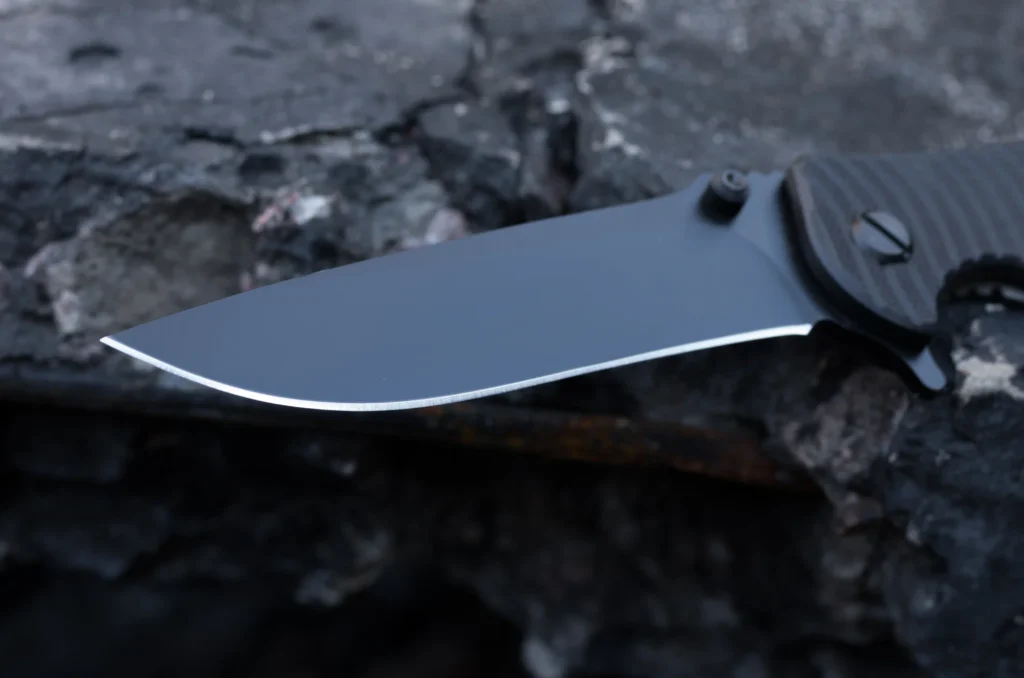
Damascus Steel
The technique of creating Damascus steel, known also as pattern-welded steel, involves forging blades from various layers of high and low carbon steel. This method results in blades with distinctive patterns and textures, making them visually appealing and highly resilient.
Damascus steel blades are highly valued for their artistry and quality, commonly found in decorative and collectible knives and swords.
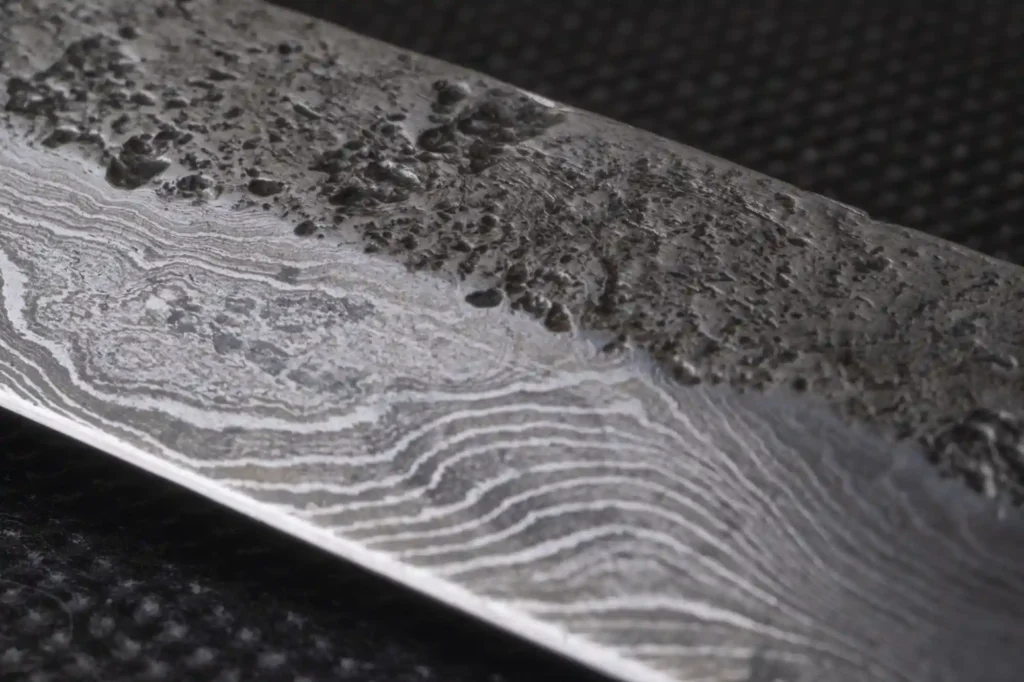
W2 Steel
W2 steel is a type of high carbon tool steel that is highly prized for its ability to maintain a sharp edge and resist wear. With a carbon content ranging from 1.05% to 1.25%, as well as trace amounts of chromium and vanadium, this steel is known for its durability and edge retention.
It is often used in the manufacturing of premium chef knives, woodworking tools, and various types of cutting instruments.
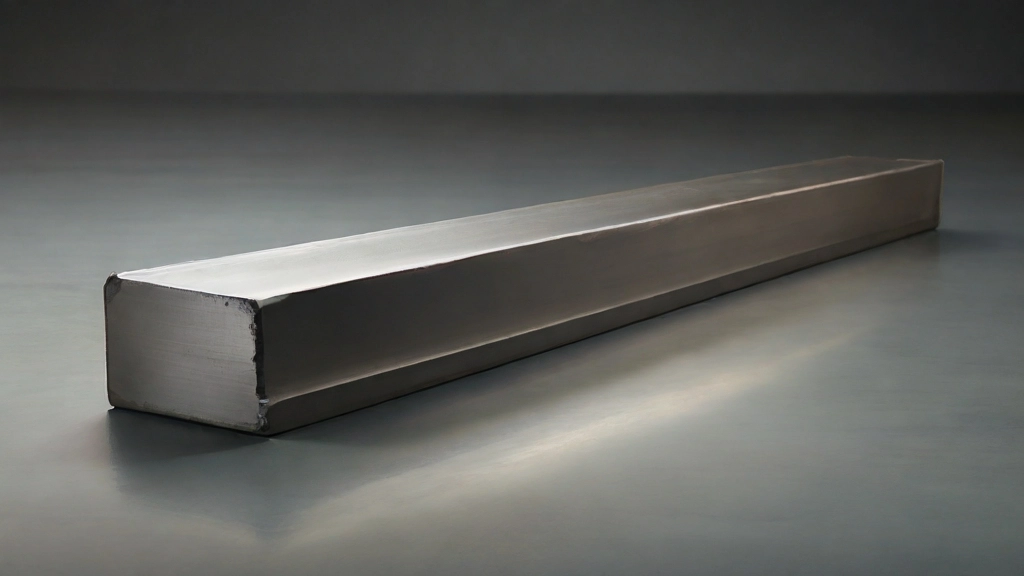
Applications in Bladed Weapons
High carbon steel is utilized in a variety of bladed weapons due to its distinctive properties that allow for exceptional performance and functionality. Craftsmen and enthusiasts alike favor this material for its versatility, making it suitable for a range of tools from ancient swords to modern knives.
Historical Swords
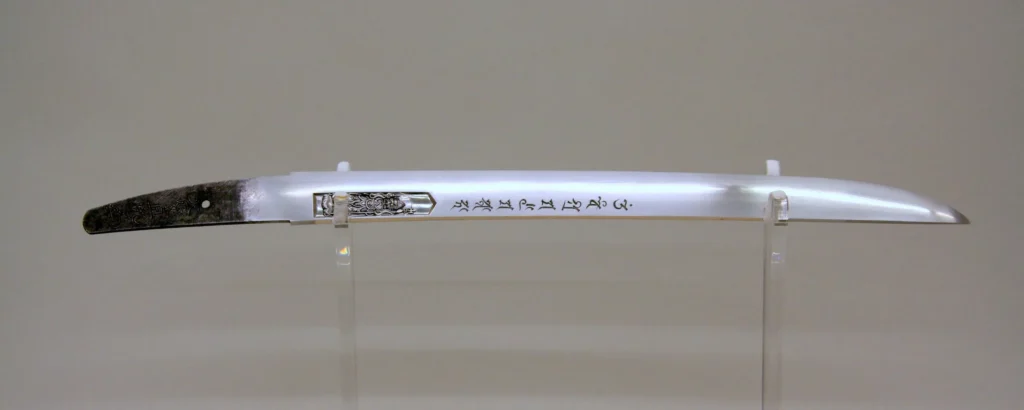
In history, high carbon steel swords have long been held in high regard as representations of authority, status, and skill in combat. High carbon steel , known for its exceptional hardness and ability to maintain a sharp edge, has been a common choice for creating swords across different societies and time periods.
Whether it be the renowned katana from Japan’s feudal era or the fabled longswords of medieval Europe, blades made from high carbon steel have significantly influenced the outcomes of battles and impacted the trajectory of historical events.
Modern Knives
High carbon steel knives are still highly esteemed in today’s world for their exceptional sharpness and durability, making them ideal for various cutting tasks. From everyday utility knives to tactical and survival blades, high carbon steel is a top choice for chefs, hunters, and outdoor enthusiasts looking for reliable performance in the kitchen or wilderness.
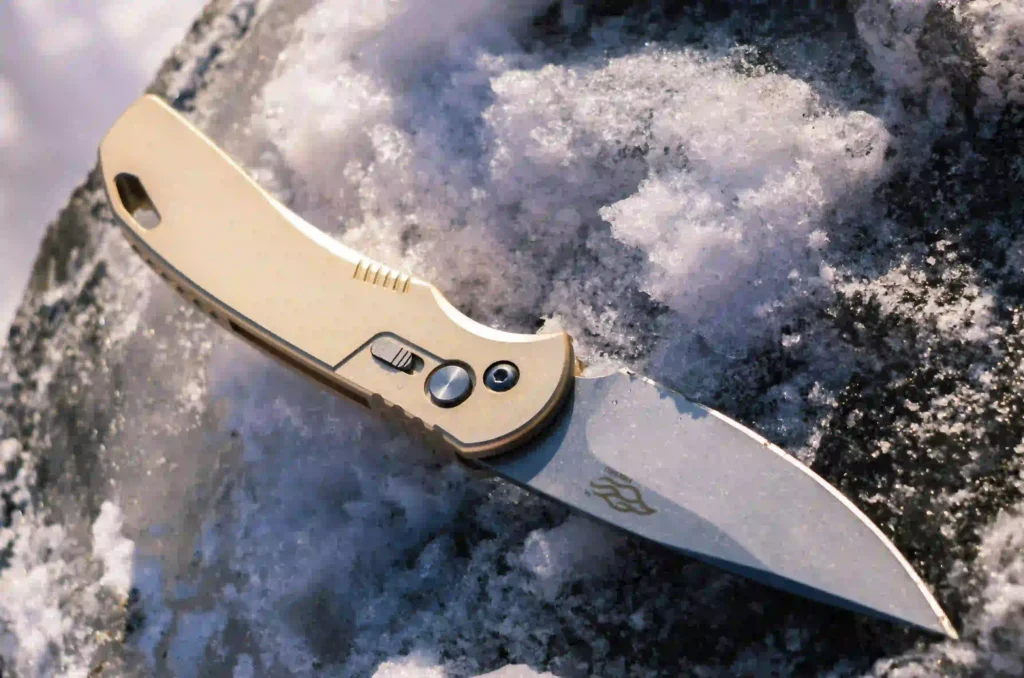
Machetes and Tools
Machetes and other cutting tools are essential implements in many cultures and industries, used for clearing vegetation, chopping wood, and performing various agricultural and industrial tasks.
High carbon steel’s combination of hardness and resilience makes it an ideal material for crafting machetes and tools that can withstand the rigors of heavy-duty use.
With proper maintenance and care, high carbon steel blades can endure prolonged exposure to harsh environments and retain their cutting edge for extended periods.
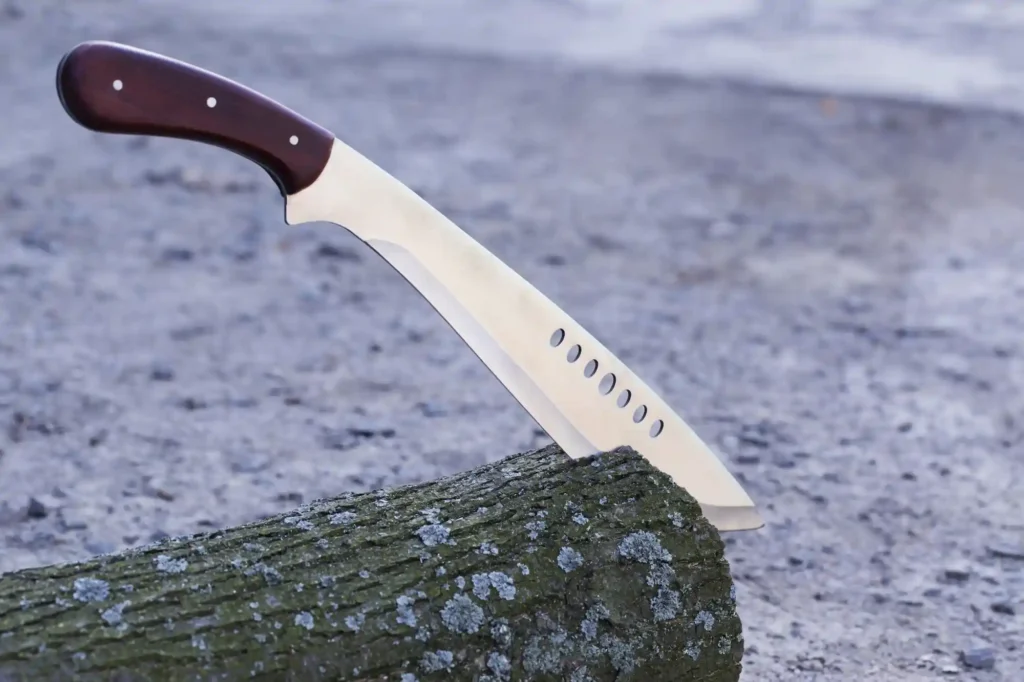
Decorative and Collectible Blades
In addition to being useful tools, high carbon steel blades carry significant aesthetic and cultural importance for collectors and enthusiasts. Artisans and craftsmen frequently use high carbon steel to create beautifully designed ceremonial blades, highlighting intricate details that represent the traditional craftsmanship of various cultures.
These blades are highly valued by collectors for their exquisite beauty, expert craftsmanship, and historical significance, often passed down as treasured heirlooms and admired as masterpieces of art.
Maintenance and Care of High Carbon Steel Blades
Proper maintenance and care are essential for preserving the integrity, sharpness, and longevity of blades made from high carbon steel. Implementing the right techniques for cleaning, oiling, and storing bladed weapons can prevent corrosion and ensure optimal performance over time.
Cleaning
It is crucial to ensure proper cleaning of high carbon steel blades to maintain their durability and performance. By regularly removing dirt, debris, and moisture from the surface, you can prevent corrosion and tarnishing that may compromise the blade’s integrity.
After each use, make sure to wipe down the blade with a soft, dry cloth to eliminate any residue. For tougher stains or buildup, a gentle scrub with a mild soap solution and soft brush can effectively clean the blade without causing damage.
Always remember to thoroughly dry the blade after cleaning to prevent moisture from causing long-term damage. By following these cleaning recommendations, you can prolong the life of your high carbon steel blades and keep them in top condition for years to come.
Oiling
It is essential to preserve the quality of your blade through the application of a protective oil layer to prevent corrosion and maintain its desired shine. Utilize a top-notch mineral oil or blade oil specifically designed for high carbon steel blades.
Using a clean cloth or applicator, uniformly distribute a small quantity of oil over the blade surface, paying particular attention to intricate patterns or etchings that are susceptible to corrosion.
Following the oiling process, allow the blade to air dry for a brief period before gently buffing it with a cloth to eliminate any excess oil. Consistently repeat this procedure, especially if the blade is regularly exposed to humid or corrosive environments.
Storage
Properly storing high carbon steel blades is crucial to preserving their condition. Experts recommend keeping the blades in a cool, dry location away from direct sunlight and moisture.
Avoid storing them in leather sheaths or humid areas, as this can cause rust and corrosion. Utilizing wooden display stands, protective cases, or blade racks is a great way to organize and safeguard the blades from harm.
Ensure the blades are securely stored to prevent accidental damage or contact with other objects. Regularly inspect the stored blades for any signs of corrosion or tarnishing, and promptly address these issues with cleaning and oiling treatments as needed.